Review of Joann’s fabrics
As a seamstress, most of my purchases from Joann’s fabrics are yards of materials. I do not believe myself to be a prestigious critic, but since I am paid for the quality of my work, I hold my fabrics and materials to a high standard. Any fault Joann Fabrics makes reflects on me in my products. For this reason, Joann Fabrics is one of the stores I will openly critique with absolute truth and experience.
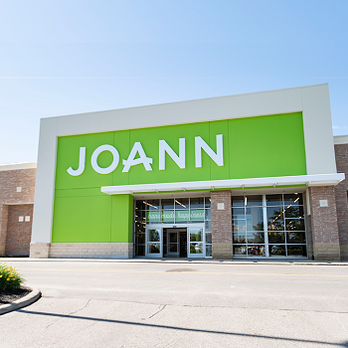
One can easily infer from the name that Joann Fabrics sells mostly fabrics. However, this is not the case. Joann’s sells all types of materials such as craft foam, stuffing, batting, needles, threads, yarns, elastics, ribbons, and much more craft supplies. In this review, I will decipher each experience I have had with purchasing from Joann’s into a concise review of 0-5 stars. The topics to which I will discuss are fabric processing/purchasing and quality of fabrics.
The processing of fabrics is unique in the sense that it is —or should be– a trained job. Processing fabrics requires knowledge on the materials. Each material has its own set of specific qualities such as durability, color and staining properties, creasing properties, composition, and much more minute facts I will not bore with. As I have observed during purchases of fabrics from Joann’s, the employees are not trained to know these and therefore make mistakes commonly. In a previous order of mine, I requested four yards of black fur (the type of fur specifically is called husky, but it has nothing to do with dogs or animal coats). Any yardage of fur is expensive, as it is a tedious process to make and keep at high quality. This amount totaled to approximately $75. For such a high price, I expected high quality. When I received these four yards, two were covered in specks of dirt, but I attributed that to the cardboard box they came in. The other two were beyond repair. Each yard appeared to have either gone through a steamer to decrease creases (of which there were still many) or had been brushed with a heated detangling tool. The microplastic filaments used to create the fur strands had been fused to one another and clustered into chunks of something resembling poorly done dreadlocks. For a material supposed to mimic the natural coat of a husky dog, this was greatly unsuitable. Not only that, but this was also avoidable. If whomever had processed the second set of yards had knowledge of the qualities of the material, heat would never have been considered and my purchase would never have been ruined.
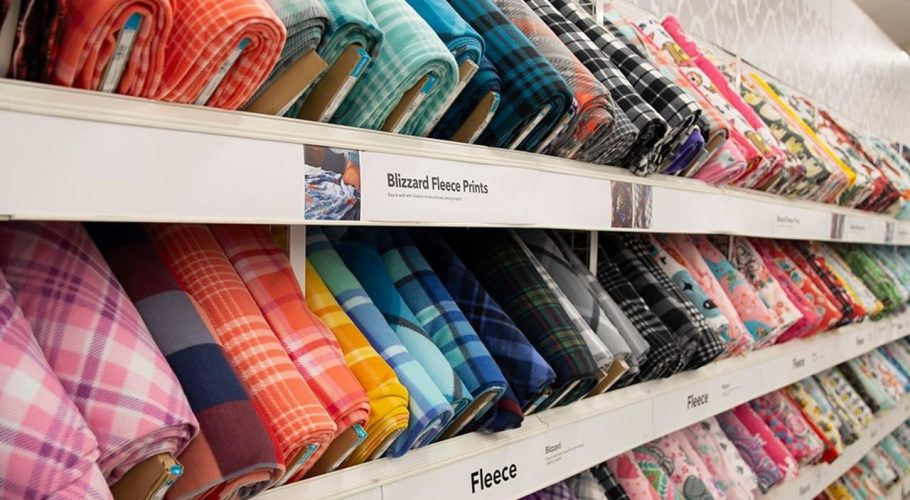
The quality of Joann fabrics depends highly on the employees. I have seen entire rolls of fabric, each containing about 30 yards, ruined because an employee creased the first layer of a delicate fabric. If a crease occurs early on, every yard following on the roll reflects the same crease, gradually increasing in size and depth with every layer. Unfortunately, the lack of care or knowledge from the employees impacts all who buy from Joann’s. A common occurrence I have seen is an employee not caring enough to cut straight lines of fabric on a particularly linear pattern. This results in the odd appearance of jagged edges and not-so-seamless finishes in a final product. Many of my projects required extra time and therefore less profit just to correct an easy line cut by an employee.

For these reasons, I rate Joann fabrics at a 2/5 stars. Nothing will beat the selection present in purchasing fabrics at Joann’s, but finding the perfect pattern does not ensure you will have a usable material. I would like to see better trained employees and more experienced staff working with processing. A store so expensive should produce materials worth their price. Joann’s fails to do this over and over, costing small-business seamstresses to lose profit.